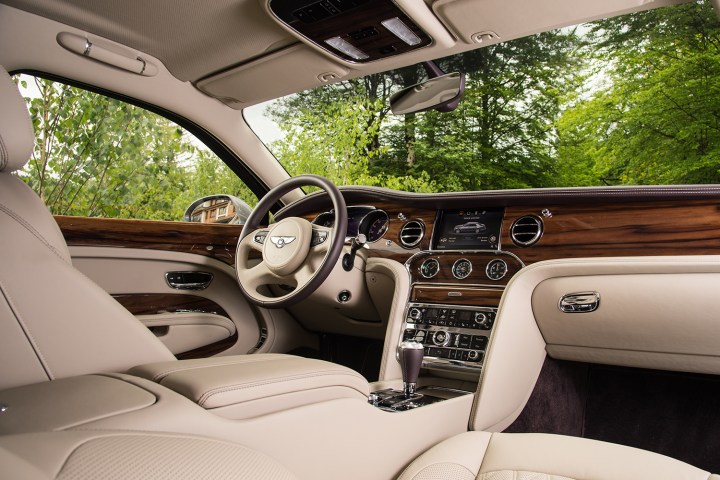
The interior of every Bentley starts with an idea. A wick of inspiration lit by a flame that can come from a diverse selection of sources. Sometimes it’s obvious; it’s easy to draw a parallel between a Bentley and a luxurious yacht. Other times it’s not as recognizable.
“How do you blend a display screen into a walnut panel? The inspiration there came from the Fender Stratocaster guitar. Sometimes you see a gloss black pick guard over a veneered body,” explained Darren Day, Bentley’s head of interior design, in an interview with Digital Trends.
He added the recent influx of technology complicates the process of designing an elegant, craftsmanship-led interior. Bentley customers expect to buy a car loaded with high-tech features but they don’t necessarily want the visual noise associated with them. They want digital detox. That’s why the second-generation Continental GT features a clever rotating screen that lets the driver choose between the infotainment system’s screen, a set of analog gauges, or an elegant wood veneer.
“Most car companies wouldn’t do that. They want to show the technology; they’re quite happy to put hundreds of buttons on the dashboard. Our philosophy is the opposite of everyone else’s,” Day told us.
Design is only part of the story. The final product must look and feel solid but, above all, it needs to be aesthetically pleasing. The Continental GT’s dashboard wouldn’t look right with Ikea-grade wood around the touch screen or pieces of shipping pallets on the doors. That’s where Bentley’s wood experts step in.
“Most car companies are quite happy to put hundreds of buttons on the dashboard. Our philosophy is the opposite of everyone else’s”
The company sources wood from suppliers scattered across the globe. Some of it comes from the United States; Bentley lists Hawaii, Mississippi, and California as major supplier states. Sourcing some species requires zig-zagging across Europe or trekking all the way out to Asia. Bentley’s suppliers know precisely where to find the seven species of wood the firm normally offers.
Finding a specific tree doesn’t guarantee a quality veneer. Logging firms send experts to hand-pick the trees that will produce the veneer Bentley seeks. They’re selected, cut down, and kept wet as they’re prepared for shipping. Letting the wood dry too quickly could damage it and ultimately render it unusable. The supplier then boils each piece for about 48 hours to soften it before shaving it into pieces no thicker than 0.6 millimeters, the global industry standard for veneer. They’re bundled and shipped to Bentley after they pass yet another quality inspection and stored carefully until the production team starts building a car.
Materials engineer Chris Thompson walked us through the process of creating a piece of wood trim. First, and significantly, Bentley uses a bundle of veneer per car to ensure a consistent finish. The pieces are mirror-matched across the grain, a process which requires an immense amount of hand-eye coordination. They then receive several glue layers and a top coat of scratch-resistant polyester to achieve the glass-like finish customers seek. The parts are then cured for several hours.
Bentley invested in a machine to polish the veneer parts it makes, though humans always supervise the process and add the finishing touch. Thompson noted Bentley goes the extra mile because the wood needs to look perfect for the full duration of the car’s life.
“I believe in the future, we will always retain a degree of wood finishes”
The amount of wood used in each car depends on the model and the options each buyer selects. Thompson noted the production team uses up to 39 square feet to build a Flying Spur equipped with the four-seater configuration and the optional picnic tables. It’s a number that hasn’t changed significantly over the past few decades. Today, Bentley found a balance between heritage and technology.
Looking ahead, the technologies engulfing the automotive industry like the evening tide promise to change the way designers draw interiors. Electrification opens up the possibility to give passengers more space; autonomy could one day give us a lounge-like cabin. Bentley believes customers will always request real wood in a car regardless of where market and industry trends take the car.
“We’re known for delivering leather and wood in all products that we sell. I believe in the future, we will always retain a degree of wood finishes,” Thompson predicted.
The types of wood Bentley offers could change over time because the firm remains committed to sourcing it responsibly. It stops offering veneers when supplies become restricted and adds new types when needed. Clients also have other choices, like carbon fiber in the V8-powered Bentayga and a stone veneer. The stone is cut so thin that it’s lighter than wood and supplies are nearly unlimited.
Stone, composites, or wood are only one part of making a Bentley. No wonder, then, that it takes about 500 hours to build a Mulsanne.