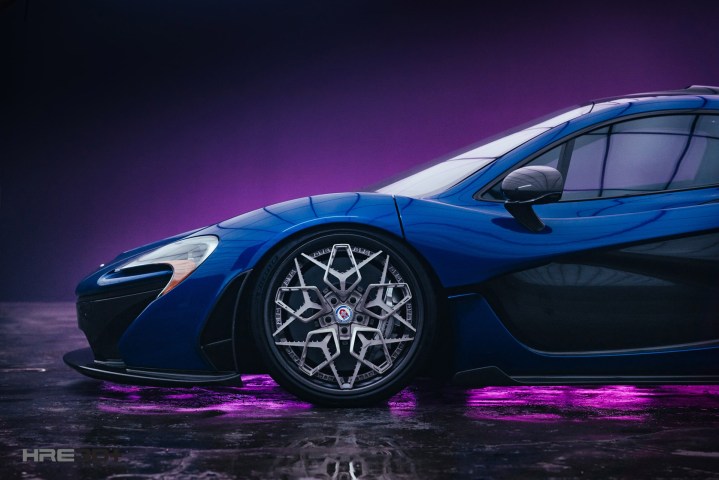
If you’re looking for the latest, greatest wheels for your precious supercar to rest upon, it doesn’t get much better than the world’s first 3D-printed titanium wheel, which was debuted this month by HRE Performance Wheels and GE Additive.
HRE3D+ wheels are made using a type of 3D printing called electron beam melting (EBM). EBM involves melting titanium powder one layer at a time with electron beams. This makes it possible to print shapes with far more complexity than with regular CNC machines. The finished wheels are not only impressively lightweight, but are also very durable, thanks to the use of titanium, one of the toughest metals known to mankind.
“The goal behind the partnership between GE Additive and HRE Wheels was to show the capabilities of additive manufacturing in a practical application,” Patrick Moran, creative director at HRE Wheels, told Digital Trends. “The aerospace industry uses additive to manufacturer a wide array of components already, but this is the first time performance wheels have been created. Currently, all of HRE’s wheels are made out of forged aluminum, and the process is time-intensive and the designs limited by the capabilities of the machines themselves and also the aluminum material.”
Compared with aluminum, titanium has a much higher specific strength and is more corrosion resistant. The manufacturing process is far more efficient, too. In a traditional aluminum Monoblok wheel, the wheel engineers start with a 100-pound forged block of aluminum and remove 80 percent to end up with the finished piece. In the case of the HRE3D+ wheels, only 5 percent of the material is removed: making this a far more sustainable process.
Unfortunately, if you’re already salivating at the prospect of being one of the first drivers to sport 3D-printed titanium wheels on your road, you’ll have to wait a bit longer. That’s because, at least right now, the HRE3D+ wheels only exist as prototypes. They were shown off at GE Additive’s booth at the Formnext trade show in Frankfurt, Germany — which concluded today — but there is still no planned date when they will go on sale.
“We don’t have a definitive answer on when we can bring this to the public,” Moran said. “Our next step will be to produce a complete one-piece center using the same process and testing from there.”