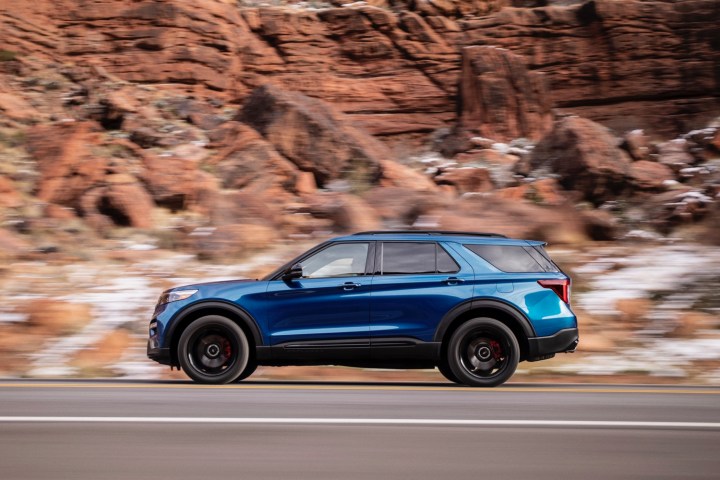
The 2020 Ford Explorer marks the first redesign for Ford’s midsize SUV in eight years. Ford has pulled out all the stops, switching the Explorer to a new rear-wheel drive platform, and adding hybrid and sporty ST models. Those are the big changes, but engineers also sweated the small stuff, as the Detroit Free Press found in a deep dive on the new SUV. These are a few of those engineering Easter eggs.
Ford shocked the industry when it decided to give its bestselling F-150 pickup truck an aluminum body to save weight. The larger Super Duty trucks, as well as the Ford Expedition and Lincoln Navigator SUVs, eventually got aluminum bodies as well. Ford didn’t give the Explorer an aluminum body, but saving weight was still a priority, Bill Gubing, the Explorer’s chief engineer, said in an interview with the Detroit Free Press. Engineers just opted to use a complex mix of materials to shed pounds, Gubing said.
Aluminum is lighter than the steel traditionally used in cars, but also more expensive. With gas prices remaining low and car buyers less interested in fuel economy, spending the extra money may not be as worthwhile to automakers, the Detroit Free Press reasoned. The new Explorer still weighs an average 200 pounds less than its predecessor, and Ford has a hybrid powertrain available to achieve better gas mileage.
Engineers also pored over every aspect of the Explorer to find ways to improve efficiency. For example, pieces of steel were cut from a tube in the chassis, saving weight by removing material that wasn’t needed to keep the chassis stiff. Hot-rodders actually used to do something similar, drilling holes in the frame rails of old Model A Fords to save weight. That was also known to weaken frames, but Ford’s engineers presumably took a less haphazard approach with the Explorer. Holes were also cut in low-stress areas of a structural rear underbody rail that’s made of high-strength boron steel.
While the Explorer is mostly steel, engineers used different grades and manufacturing processes depending on how strong a specific part needed to be. The Explorer also has some aluminum parts, and engineers used different manufacturing processes (casting, extrusion, heat treating) for those as well. Magnesium was used in the radiator support and a beam that runs behind the dashboard, saving additional weight. Engineers even made the plastic in the air conditioning ducts thinner.
The dashboard has dual-wall construction, with an air gap between the two walls. This eliminates the need for heavy sound-insulation padding, but still keeps the cabin quiet. The wall between the passenger compartment and engine compartment is also dimpled — like a golf ball — to reduce noise and vibration. Based on our recent first drive of the 2020 Explorer, we can say that these details add up to a very capable and refined vehicle. It shows how much engineering goes into even the most mundane family hauler.