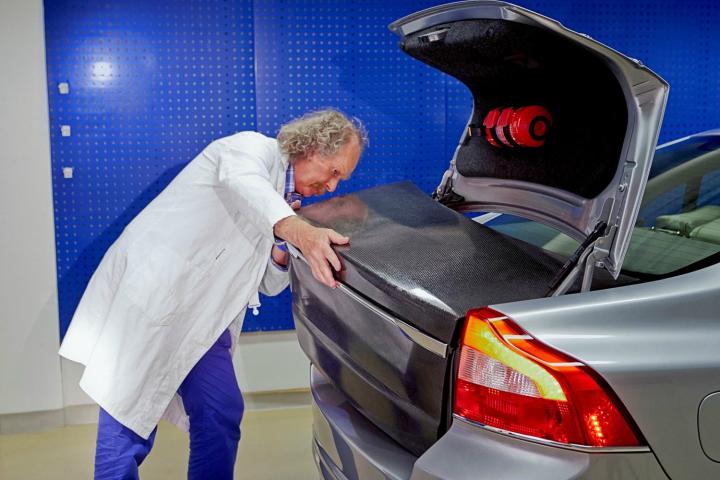
Batteries suck. They are big, heavy, not very environmentally friendly to produce, and very expensive. But unless hydrogen cars become ubiquitous, we are stuck with them. Or are we?
Volvo has just come with a technically complex but incredibly intuitive solution; mold the batteries into the body and frame of the car. This has tremendous advantages in increasing the total storage capacity of the car while simultaneously making it much lighter.
The technology behind this development is staggering, and would take someone with degrees in materials science, electrical engineering, and possibly theoretical physics to understand and explain properly. I have a JD and haven’t taken a science class since freshmen year of college so bear with me.
Layers of polymer resin are sandwiched between carbon fiber, to create a super-capacitor. The carbon fiber layers are charged as conductors and the resin acts as a neutrally charged dielectric.
These millimeter thin capacitors are then molded into carbon fiber body panels. Such capacitors have a much higher energy density than typical lithium-ion batteries and are capable of much quicker recharge.
To top it all off, Volvo estimates that if these materials were used throughout the car in place of a steel frame and body panels the vehicle’s weight could be reduced by as much as 15%. This makes sense, because as we know from supercar manufacturers the use of carbon fiber makes anything at least 28 percent more awesome.
Now that’s a technology Nikola Tesla would be proud of.
Currently Volvo is running tests with one of their S80s, on which the trunk and plenum/rally bar have been replaced with the new energy storage panels. These two alone are enough to run the cars entire 12-volt electrical system.
The bad news is that it has taken Volvo three years to get this far, and the technology development is not what anyone not named Bill Gates would call cheap. There is no way of knowing for sure that this technology will be technically or economically viable, but the benefits are clearly there to see.
The 85 kW-h battery back in the excellent Tesla Model S weighs around 1300 pounds, and has to be this heavy to achieve its EPA rated range of 265 miles. That’s the same effective energy density as a 30mpg car would get from 75 pounds of gasoline. Now some of that weight is made up for by the fact that the Tesla isn’t hauling around an engine block, but still the problem is there to see.
If you want to go further, the batteries get bigger and heavier meaning you need still more of them to carry the increased weight. This is called a negative spiral, Volvo’s technology offers a positive spiral in which reduced weight of batteries means you need fewer and fewer of them as the vehicle gets lighter.
Lastly the fact that Volvo is making this technology reassures me. Volvo engineers are pathologically obsessed with safety, to the point where their stated goal is to have statistically zero fatalities involving Volvo cars by the year 2020. This makes me think that if they go forward with the technology you aren’t likely to be electrocuted opening your door, or burst into flame when you outwit the safety features and run into a post.