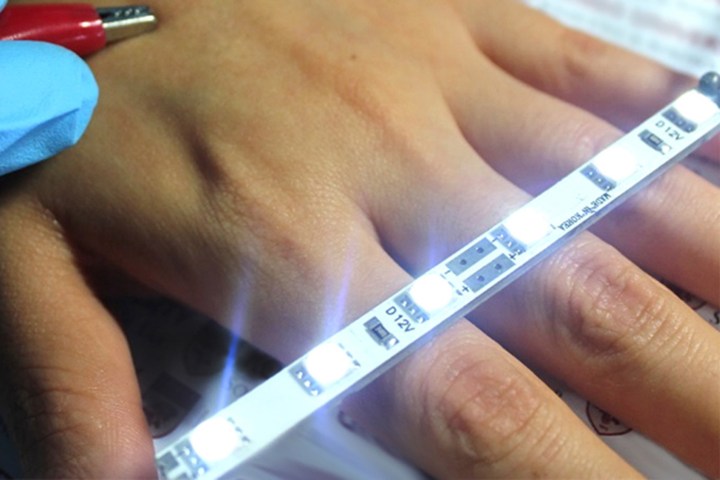
Like most electronic skin materials, the ultra-thin film is transparent and highly conductive. Described as a “self-junction copper nano-chicken wire,” the e-skin material is a tangled nanofiber mat of polyacrylonitrile (PAN). The fibers of this material are very thin, measuring one-hundredth the diameter of a strand of human hair. “The fiber shoots out like a rapidly coiling noodle, which when deposited onto a surface intersects itself a million times,” said UIC professor and study co-author Alexander Yarin in a prepared statement.
Related: MIT researcher’s artificial skin will make you look 10 years younger
This electrospinning process creates a fibrous material that is very lightweight and transparent. It also allows it to be flexible and durable. The film can retain these properties even after repeated bending and stretching, making it ideal for wearables, roll-up touchscreen displays, and more.
Once the PAN fibers have been spun, they are ready for the next phase of manufacturing that adds conductivity to the otherwise electrically inert material. The researchers first spatter-coat the fiber with metal that will attract metal ions, and then electroplate it with copper (or silver, nickel, or gold). The resulting film has a “world-record combination of high transparency and low electrical resistance” that is ten times greater than the existing record, claims Korea University professor Sam Yoon. The conductive skin also can be applied to any surface, including skin, glass, and more.
The biggest advantage to this electric skin is how it is made. The two processes used to make it — electroplating and electrospinning — are standard manufacturing techniques. Each step uses existing materials and only takes a few moments to complete. These factors make it possible to scale the production of the material rapidly and efficiently. Both the discovery and development of this electronic skin was described in the June 13 issue of Advanced Materials.