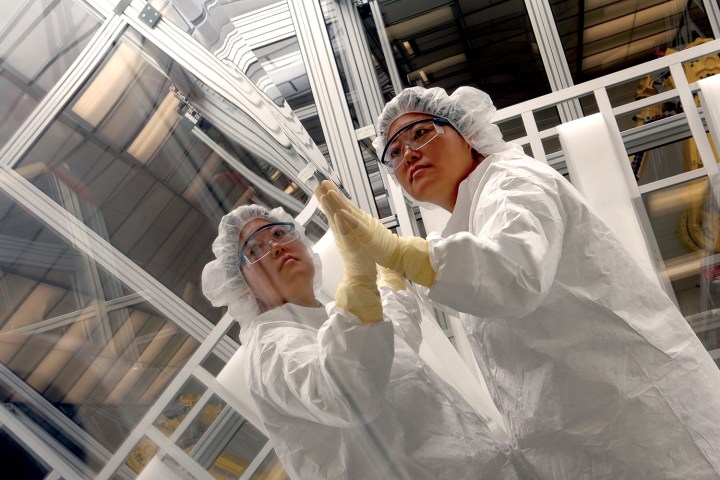
The name Corning is synonymous with glass and with good reason.
Corning developed the bulb-shaped glass for Edison’s incandescent lamp; Corning’s heat-resistant glass made safer railroad lanterns, technology that evolved into car headlights; CorningWare and Pyrex provided temperature resistance in kitchens and labs; and its glass ceramics were even employed in the nose cones of space ships.
Today we associate the name with Gorilla Glass, which is widely used in the mobile industry, but Corning is also a big manufacturer of display glass for TVs, optical fiber for communications, and the glass in catalytic converters for cars. The company recently unveiled Valor Glass, a new glass packaging product for use in the pharmaceutical industry, and it’s making further inroads in the automotive sector with car exteriors and interiors.
“We are really driven by this belief that we can continue to make life-changing innovations,” Chief Strategy Officer Jeff Evenson told Digital Trends. “We see a material with almost unlimited potential. We can make it strong, we can adjust its optics, we can adjust its chemical properties, we can adjust its thermal expansion behavior or lack thereof, we can adjust its electronic properties, and obviously we can adjust its color and other aesthetic properties.”
166 years of expertise
Now in its 166th year, Corning has 107 facilities and employs more than 45,000 people. Its global headquarters and research and development center is, naturally, based in Corning, in upstate New York, but it has facilities and employees all over the world. Most recently the company acquired an empty, million-square foot plant in Eugene, Oregon, which was previously the Hynix computer-chip plant. Corning has yet to reveal what it plans to make there.
While Corning is a household name, much of the work it does is behind the scenes, producing glass that goes into other manufacturer’s products. Most of its $9.4 billion sales in 2016 were generated by producing glass layers for TVs, and optical fiber strands for telecommunication networks.
“The display industry is our largest business in terms of sales and earnings,” Evenson said. “We account for a little bit more than 50 percent of the glass that goes into all televisions around the world.”
“We see a material with almost unlimited potential.”
Its Gen-10.5 glass technology allows the company to make a piece of glass that’s as thin as a business card, has the area of roughly two king size beds, and is flat to within 200 atoms all over without polishing. It’s not something that can be practically shipped, so Corning builds its factories contiguously with panel maker’s enormous plants.
“The main TV in someone’s living room continues to grow larger, and that’s the biggest trend and driver of volume for us,” Evenson said. “These large pieces of glass allow manufacturers to make large TVs much more cost effectively.”
The same manufacturing techniques are employed for the increasingly tough Gorilla Glass that covers many of our smartphones, and the display glass inside them, though the formulation is different.
“Our second largest business is optical communications,” Evenson explains. “Worth in excess of $3 billion in sales, we sell not only optical fiber, but a lot of the connectors and cables that go around it.”
Corning advanced the development of optical fiber in 1970 after winning a competition issued by the British Post Office Telecommunications department, which would later become British Telecom, to create a light pipe that could keep at least 1 percent of the light over a kilometer. Corning scientists used a technique called vapor deposition, originally developed to produce high quality glass for telescope lenses, to create strands of glass with very high purity.
“They were really focused on low thermal expansion, and what they observed was that the irregular expansion you’d get in normal glass that you’d have in a window was caused by impurities,” Evenson said. “They realized that you’d have to start with gasses instead of sand to control the purity. So, they learned to turn the gasses into a solid and then eventually remelt the solid and make it into a glass and that’s how optical fiber is made.”
Last September, Corning passed its billionth kilometer of optical fiber sold. It has been investing heavily in fiber plants in North Carolina and elsewhere to support higher levels of production ahead of the shift to 5G. Verizon has already agreed to a $1.05 billion three-year minimum purchase agreement for Corning to provide fiber optic cable and associated hardware to help it improve coverage and speed the roll out of 5G capabilities.
Venturing further into pharmaceuticals and autos
“Our next big business is environmental technology, built on the invention in the 1970s of extruded ceramics that can put the area of a soccer pitch into the volume of a soda can,” he said. “That has dramatically reduced emissions from cars, not only cars with internal combustion engines but also hybrid electric vehicles.”
This long-standing relationship with auto manufacturers has led Corning to think about where else glass might improve cars. We went to see Corning’s glass concept car at CES last year. Externally, the company is using Gorilla Glass to make lighter windows, which can provide better fuel economy or longer range in electric cars, and higher performance because lighter cars with a lower center of gravity can accelerate and brake more rapidly.
Gorilla Glass can be used to make clearer and more durable windshields, better able to deflect rock strikes without damage. Corning can also put an electronically controlled opacity film between the layers of glass to tint your car windows at the push of a button.
“For the interior of cars, it gives you a highly durable surface and allows car manufacturers to make an interface with the same responsiveness as a smartphone,” Evenson said.
This could enable new curved interior designs and even entire dashboards that can function as touchscreens. Corning is currently working with “25 auto platforms globally.”
“There are questions we’ve been asking at Corning that we’re closer to providing definitive answers to.”
The latest Corning product to hit headlines is its new Valor Glass, developed for the pharmaceutical industry. Back in 2011 the U.S. Food and Drug Administration (FDA) released a paper that highlighted problems with glass vials. Interactions with the liquid inside can cause flaking, particles that shouldn’t be there can get in during manufacturing, and breakages cause frequent recalls.
Corning worked with Merck and Pfizer to develop damage-resistant glass that’s more efficient to manufacture and far less prone to contamination. It’s investing heavily to build facilities that will make this new aluminosilicate glass packaging and expects it to grow into a big business fast.
Seeking glass innovations
This new direction came about because Corning CEO Wendell P. Weeks also had a seat on the board at Merck and saw the problem. Because the applications for glass are so varied, Corning is constantly looking for new possibilities and partnerships.
“Sometimes you have an event like the British Post Office Telecommunications competition explaining to the world exactly what they need,” Evenson said. “Sometimes you have somebody like Steve Jobs realizing that to make the original iPhone, a plastic cover was insufficient, and he needed something that offered more scratch resistance.”
Jobs was annoyed that plastic scratches too easily, but he felt glass was too prone to cracking. He got wind of Gorilla Glass, but Corning wasn’t ready for mass production. In typical Jobs style, according to Walter Isaacson’s biography, he put in an order and gave Corning six months to produce enough cover glass for the original iPhone. Now in its fifth generation, Gorilla Glass has been used in more than 5 billion devices to date.
“Our relationships with companies have now evolved to the point that we share roadmaps with each other and that informs our research direction, Evenson said. “One area we don’t talk about much, but where I think glass could become incredibly valuable, is in the semiconductor industry to build high performance servers, switches, and routers.”
As people try to pack more transistors into a smaller volume by stacking chips, they need something in between that allows for electronic insulation needed while preserving the thermal properties of the silicon. Evenson thinks glass could be ideal and Corning is already working on glass interposers, though he admits it’s very early days for this kind of technology.
“We have lab reports going back 100 years. There were things 80 years ago that had no scientific limit, but there were practical limits at the time, and now we’re seeing advances that allow you to do those things,” Evenson excitedly said. “There are questions we’ve been asking at Corning that we’re getting closer to providing definitive answers to.”
One thing is for sure: Corning will continue to try and develop new glass innovations everywhere it sees a potential opportunity.